|
Pipe Extruder Machine
|
|
|
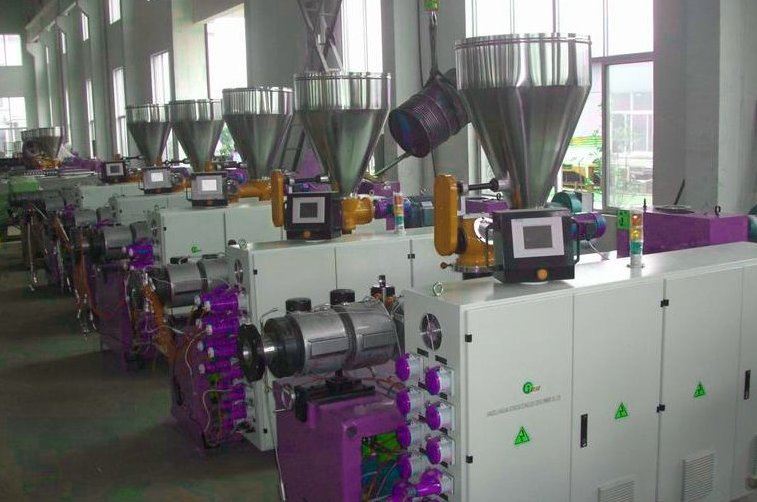
Pipe Extruder Machine is responsible for manufacturing high volume products in which raw plastic material is first melted and the formed and given a shape into a regular shape. This machine is known for producing high quality weather stripping products, pipe/tubing, deck railings, fencing, plastic films, window frames, thermoplastic coatings and many more products in the form of wire insulation.
Process:
During the extrusion process of plastics, the raw material the form of small beads or resin is being gravity fed into the barrel of the extruder through a top mounted hopper. After that, additives like UV inhibitors and colorants in pellet or liquid form are widely used, which is further blended into the resin before it arrives at the hopper. This process is related and common to plastic injection molding as seen from the point of extrusion technology. However, it differs as it is a continuous process. The pultrusion process is known to offer similar profiles that too in continuous lengths, generally with added reinforcing, which is attained by pulling the end-product out of the die rather than extruding the polymer melt with the help of die.
In Pipe Extruder Machine the raw material enters through the fed throat, which is an opening close to the rear of the barrel; and then comes into direct contact with the screw. The rotating screw that normally turns at up to 122 rpm gives momentum to the plastic beads and pushes is ahead into the heated barrel. The preferred extrusion temperature is seldom equal to the already set temperature of the barrel owing to viscous heating process and other various effects. Generally, in most of the cases, a heating profile is arranged for the barrel, which has three and more independent PID controlled heater zones that steadily increases the barrel temperature from the rear to the front where the plastic enters. This permits the plastic beads to melt in a swift way as they are influenced through the barrel, which eventually outlaws the question of overheating.

|
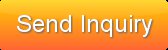 |
|
|
|
|